JSC Gandras Energoefektas more than 10 years successfully co-operate with company Plenty, who is a leader in mixers market.
We’ll offer you the best mixers with the following installation possibilities:
- Top Entry
- In the pipeline
- Side Entry
- Submersible mixer
Our company supplies two types of mixers:
- Fixed-Angel
- Swivel-Angel (mixer angel of entry can be varied by means of mechanical (manually) or electrical actuators (for continuous automatic angel of entry changing). The motor and mixer shafts are connected by a belt drive or gearbox.
Mixers, supplied by our company, are indented for mixing, preparing and storage of:
- Oil products (machine oil, petrols, diesel oils, fuel and bunker oils);
- Vegetable oils (sunflower-seed oil, olive oil, colza oil, palm-oil…)
- Yogurts
- Milk cocktails (for industrial production only)
- Mayonnaise
- Alcoholic drinks (cocktails, vodka, cognac, whisky, liqueurs, vermouths, rum, gin)
- Wastewater
Our supplied mixers advantages, using mixers in Crude Oil and Heavy Oil Storage Tanks:
- you can control and prevent the accumulation of bottom sludge and water pockets in crude oil storage tanks;
- you will maintain homogeneity of refinery finished or intermediate products (mixing two or more products). Heavy fuel preparation for firing;
- water with fuel oil content utilization
- screw pump protection from entry of the water
- waste products cleaning from the crude oil and heavy oil storage tanks
- heat transfer. Mixers improve efficiency and reduce costs for heavy oil heating. (Mixer design (possibility to change angle of entry inside the tank automatically) allows to reduce the time for heating by 35-45% and to reduce the energy consumption by 3-5%. Sand accumulation, fuel oil agglomeration and coke generation is entirely excluded).
- mixer design allows to carry-out servicing (replacement of bearings, mechanical seals, belt, reduction gear) without draining the tank.
Our supplied mixers differences from other companies’ mixers
1. Servicing. Original cut-plate construction of our supplied mixers allows to carry out maintenance (replacement of mechanical seal, bearings etc.) without draining the tank.
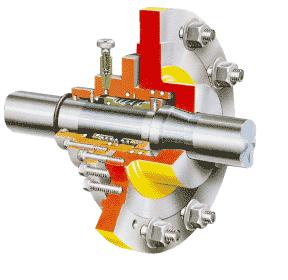
2. Bearings. Mixers are completed with standard bearings and mechanical seals. The bearings of our supplied mixers are in oil reservoir outside the tank and do not require maintenance. Mean lifetime - 40000 hours.
3. Impeller design. The high efficiency type true helical pitch impeller with forward rake is specially designed for effective and controllable flow. Each impeller is accurately cast as one-piece component and ensures reliable operation. If mixer is selected correctly, there is no need to dismantle impeller during mixer mounting.
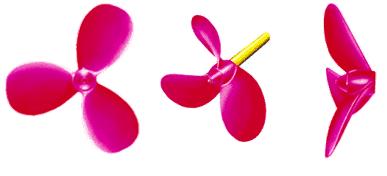
4. Belt-drive, reduction gear. Beside reduction gears, our suggested mixers are completed with antistatic belt-drive, which has the efficiency of 98-99%. The belt design excludes the slippage effect entirely. The belt is easily reachable (it is on the mixer and motor shaft end), protected by spark proof and weatherproof guard, which is removable without any special devices.
JSC “GANDRAS ENERGOEFEKTAS” produces mounting flanges for all types man-holes (oval, round, square). You would need just to screw the nuts!