- Simple construction and maintenance;
- High reliability;
- High deaeration effect at a temperature t=76-80˚С;
- Fully automatic process.
|
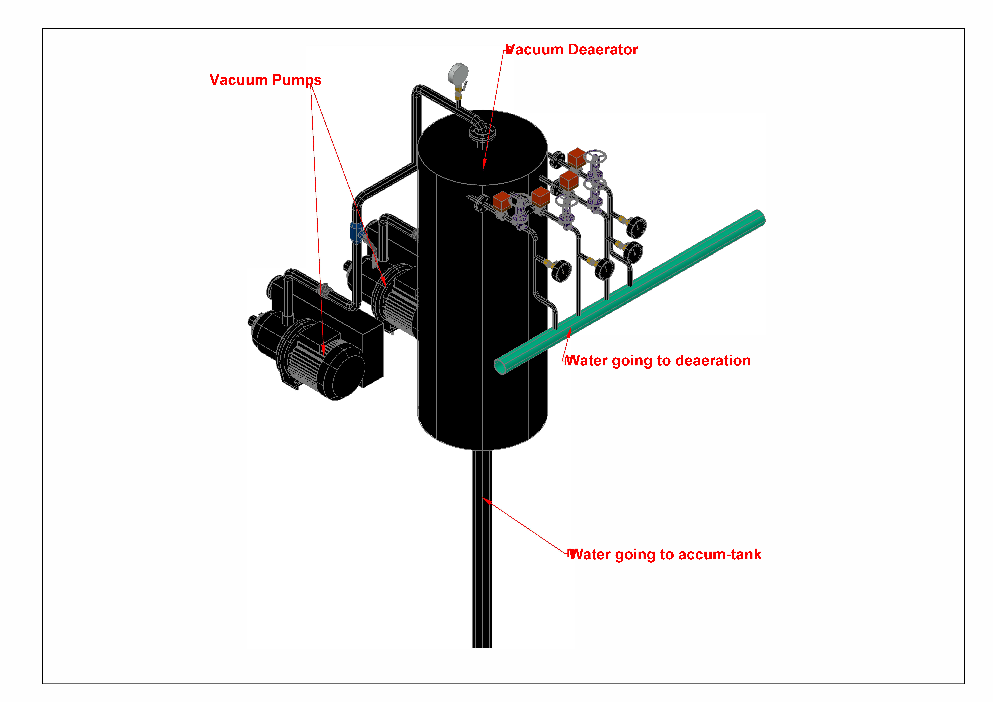 |
Vacuum deaerator technical data:
Rated capacity, m³/h |
7, 15, 35, 50, 100, 150, 200 |
Nominal temperature of treated water before deaerator, ˚С |
75-80 |
Nominal treated water pressure before vacuum deaerator, Bar |
4 |
Nominal treated water pressure before vacuum deaerator, Bar |
-0,5 |
Concentration of dissolved oxygen before deaerator, mkg/l |
>8000 |
Concentration of dissolved oxygen after deaerator, mkg/l |
<50 |
Short description of water vacuum deaeration system operation:
Chemically cleaned water flow with temperature 20°С goes through heat-exchanger thus is being heated by system water flow with temperature 75-80°С (summer time they use water from the recalculating line of water heating boiler) and then goes to working nozzles of vacuum deaerator.
Vacuum deaeration system can operate in different modes. The rated output of every mode and number of modes are determined after receiving detailed technical specification for design.
It is possible to regulate the output by the receiving signal from the level gauge which is mounted on the hot well.
When the chemically cleaned water goes through the working nozzles it boils and then begins to discharge the dissolved corrosive gases (О2, СО2).
Deaeration and discharging corrosive gases removal are realized by the vacuum pump.
The pressure of vacuum deaerator is (-0,5÷-0,8) atm (by vacuum-gauge). Deaerating water flows after vacuum deaerator to hot well. Minimal volume of hot well is 5-10% of maximum deaerator output rate. It is possible to supply any other volume hot well according to the customer’s choice.
Deaerating water from well to accumulator tank or boilers is supplied by deaerating water pump.
Discharging corrosive gases remove by the liquid-packed vacuum pump from deaerating column and deaerating tank to cold water tank. The system has two pumps, one working, and another reserve. Cold process water with temperature 15-20˚С is used as sealing water of vacuum pump. The cold water pumps from cold water tank.
After vacuum pump discharge water and water mix with corrosive gases flow together to the tank of vacuum pumps. Hot water with temperature 50-60°C pumps to cold water piping before heat-exchanger by Q=1 m³/h., H=60 m.v.st pump. The system has two pumps, one working, and another reserve.
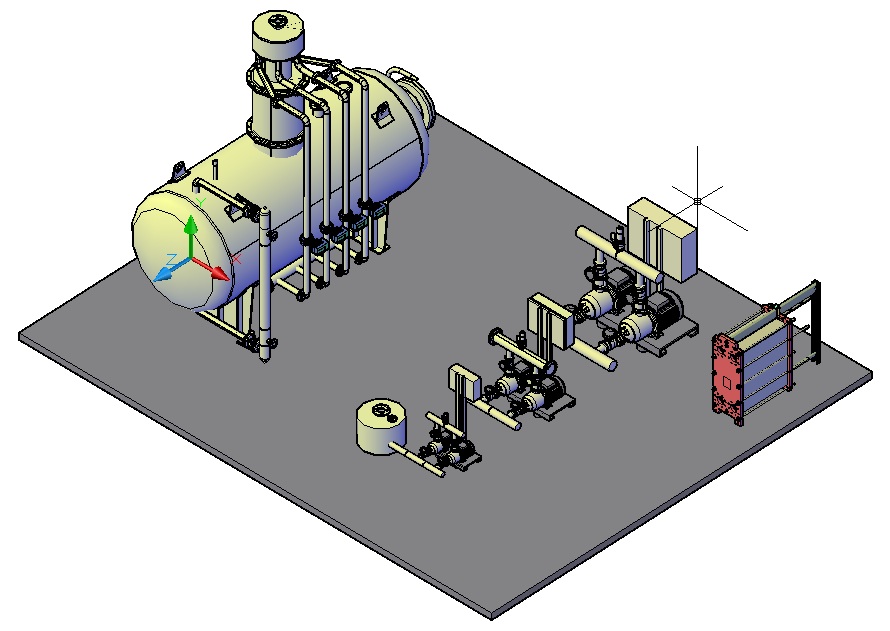
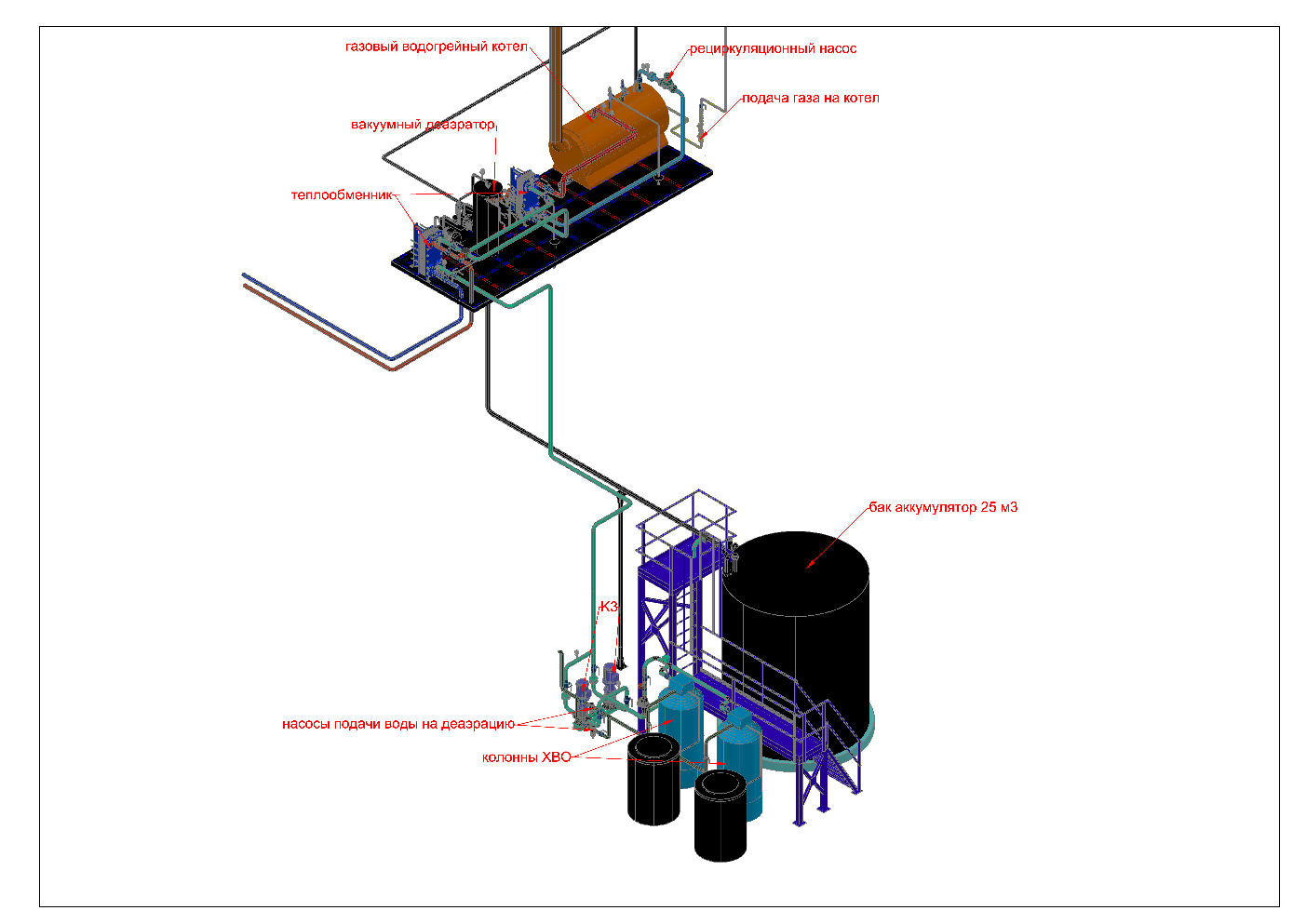